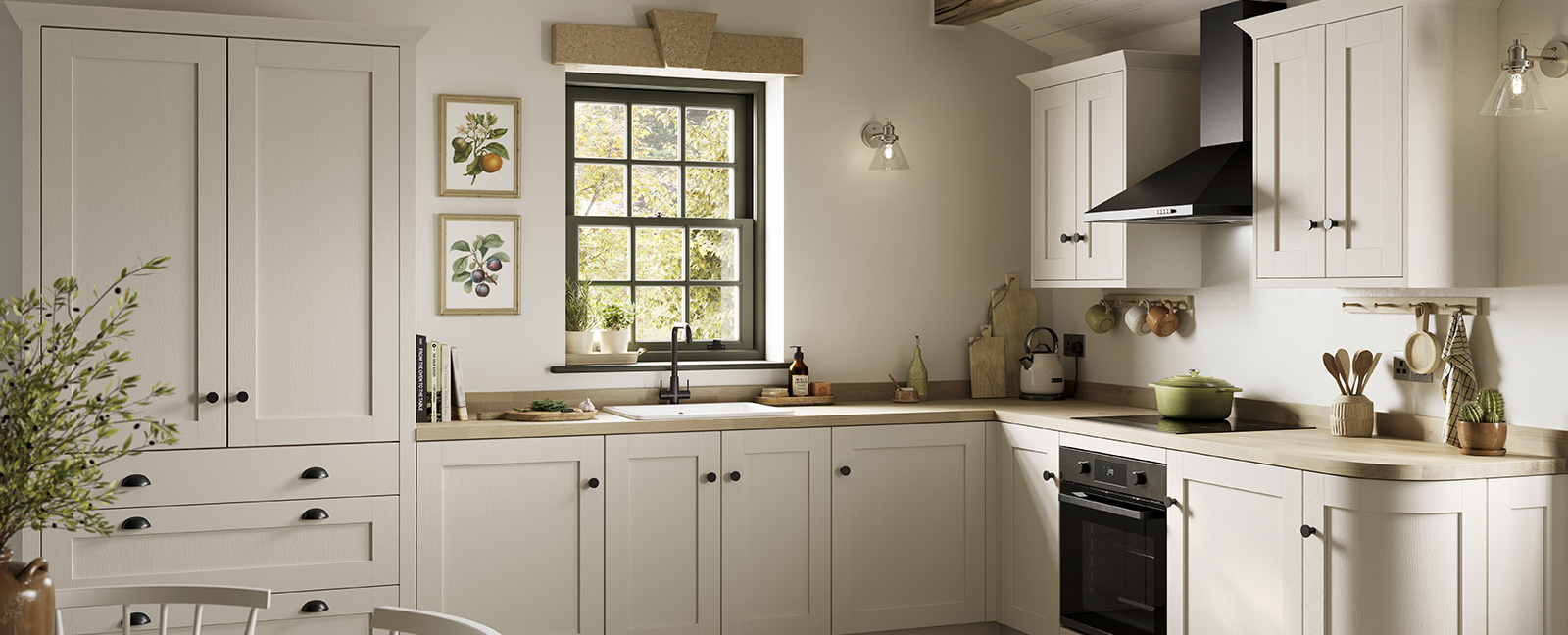
Product offer and innovation
Energy-efficient, safe and durable product, where sustainability considerations are built in as a pillar of the design process, helps to mitigate our ‘Product design relevance’ risk.
Sustainable product offer and product innovation
Our ambition is to create sustainable products that we’re proud of. We make almost 5 million cabinets a year in our own UK factories, so this is a product where our choices can make a real difference. We buy our chipboard from sustainably managed UK forests. For every acre of trees used, an acre or more is planted.
When the cabinet has come to the end of its life in the home it can be recycled and broken down to produce more chipboard, which can be used to make more cabinets in the future.
We don’t only want to do things to an incredibly high standard – we want them to be sustainable too. Sustainability is built into our product design process and is one of our five standard pillars that we base new product design and sourcing decisions on, sitting alongside quality, design, cost and availability.
Some recent examples of building sustainable considerations into new product are shown below.
1 Cabinet guarantees and recycling
The product that sits at the heart of our business, all our cabinets come with a 25-year guarantee. We can offer that because we know quality and longevity are built into the design. We hold the furniture industry (FIRA) gold award for product excellence for our rigid cabinets. They are also 90% recyclable at end of life. The chipboard in our cabinets is made using 35% recycled content. The cabinet feet are made of 100% recycled plastic and are 100% recyclable at end of life.
2 Recycled laminate worktops
Our own-manufactured laminate worktops are now made using 75% recycled content.
3 New developments
We are always looking for ways to improve the environmental impact of our products. Notable developments in 2023 are:
- Our new Halesworth frontals are made using 50% less plastic, resulting in 50% less CO2 emissions.
- Our bestselling Greenwich Matt frontals are now 100% recyclable.
4 Plastic pledge
Our ‘Plastic pledge’ is an initiative looking across all the products we sell, and aiming to reduce, remove, and replace plastic in our packaging wherever possible. Finding plastic-free replacements for some elements of packaging can be difficult because the product has to be protected all the way through the supply chain from manufacture to end-user. We are very pleased to have launched our first Lamona own-brand appliances with polystyrenefree packaging. Polystyrene is not commonly recyclable in domestic waste collections, and where it is recycled it takes a lot of energy to break it down. We’ve managed to find a solution which replaces the polystyrene with cardboard but which still offers the protection that our customers need.
In 2023 we removed approximately 300k pieces of polystyrene from the products we sold. Our aim is to increase this figure as we find more wins across the product range.
5 Eco washing machines
On Lamona washing machines, we worked with our third-party manufacturer to make the eco setting the default setting for the wash programme. This is not the case on all other brands. We work hard to build reliability into all our own-brand Lamona appliances and we’re proud to back that up with a 3-year warranty as standard. Where we have warranty claims we encourage end-users to accept our offer of sending an engineer to repair their appliance rather than replace it under the terms of the warranty. This happens in over 90% of claims.
Responsible purchasing
Each potential supplier undergoes a thorough risk assessment and we have successfully implemented SAP Ariba SLP (Supplier Lifecycle and Performance) to enhance our supplier onboarding process. We use SAP Ariba to reassess our legacy suppliers to ensure continued alignment with Anti-Corruption, Human Rights goals, sustainability, and the Company’s code of ethics.
We continue to adopt the SEDEX (Supplier Ethical Data Exchange) platform as our tool of choice for gaining visibility and assurance over these principles through the four risk pillars adopted by SEDEX: labour standards, health & safety, business ethics, and environment practices. We use SEDEX RADAR risk assessment tool to make an informed decision on the supplier’s ability to meet the HJ Supplier Code of Conduct.
All our buyers and our compliance team have taken and passed the Chartered Institute of Procurement and Supply’s Ethical Procurement & Supply training, and we have a rolling programme of refresher training on Modern Slavery, Anti-Bribery, Timber Legality, FSC® and PEFC chain of custody and the SEDEX RADAR tool. We are also members of Timber Development UK and are recognised by them as a ‘Responsible Purchaser’, which means that we have third-party assurance on our timber purchasing due diligence systems.