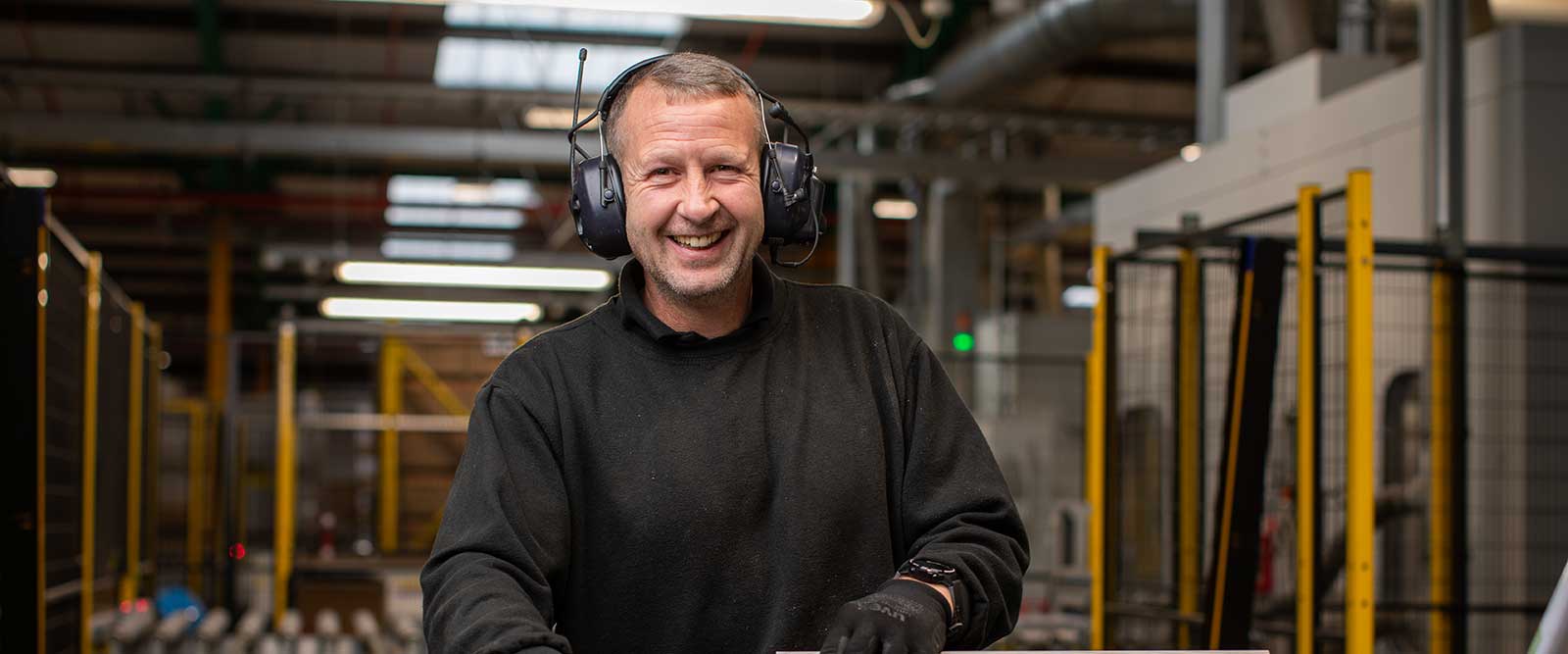
Keeping people safe
We have over 12,000 employees and we want all of them, along with our contractors, visitors and customers, to stay safe all the while they are at our sites.
Health and safety
In 2024, our safety KPI remained low at 176 RIDDOR reportable injuries per 100,000 employees. This is 19% below the 2023/2024 HSE All-Industry rate of 217. Our accident severity rate has also remained low at 28.8 hours lost to accidents per 100,000 hours worked.
Our network of depots in the UK and Republic of Ireland was awarded the ISO 45001 certification in early 2022 and continues to hold this. This was achieved by implementing simple and visual safety management systems and actively encouraging the participation of all staff to help continuously improve Health & Safety (H&S) performance. We have also held ISO 45001 certification across our manufacturing and distribution network since 2009.
Across the business we continue to work hard to embed the cultural value that safe operations is our way of doing things. In 2023, we introduced H&S recognition initiatives, such as the ‘Safety Good Spot’ and ‘Local Safety Hero’ Awards, celebrating the positive impacts of employee participation and proactive behaviour.
To maintain momentum on our safety culture improvement plan we have partnered with the Centre for Human Factors (CFHF) at the University of Hull. The CFHF are working with us to help benchmark our safety culture maturity and identify possible action plans for the future.
HOWDENS Making space more valuable
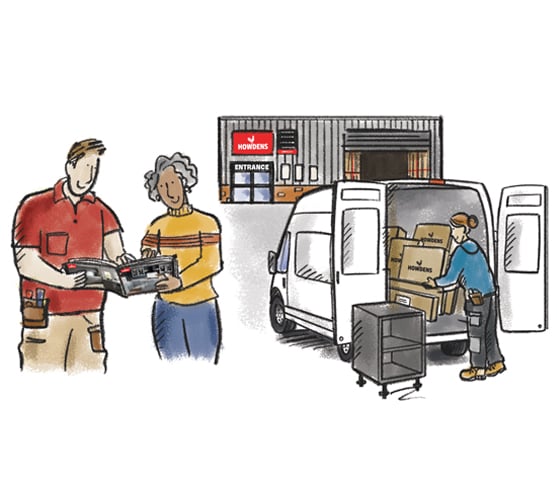
Business Model and Strategy
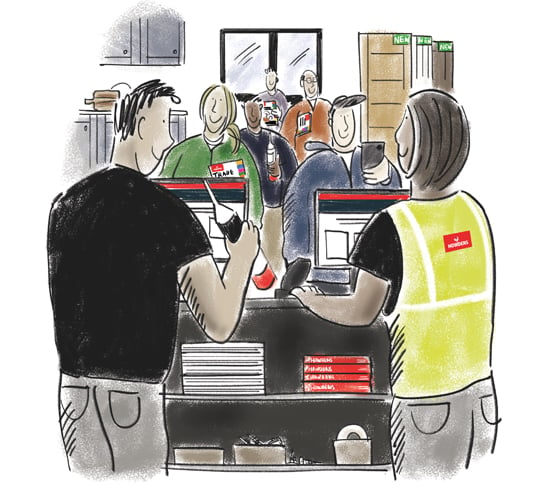
Depots
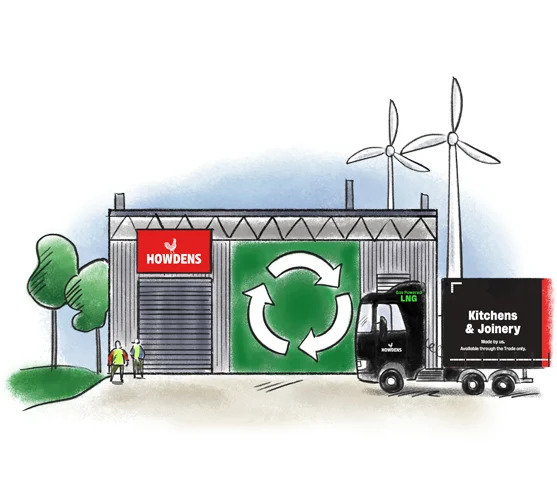
Sustainability
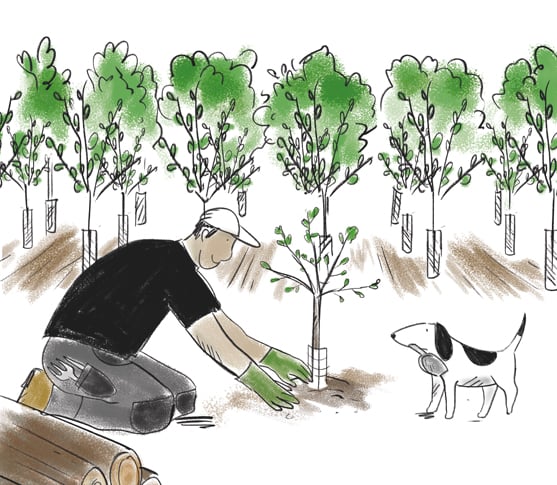
Community
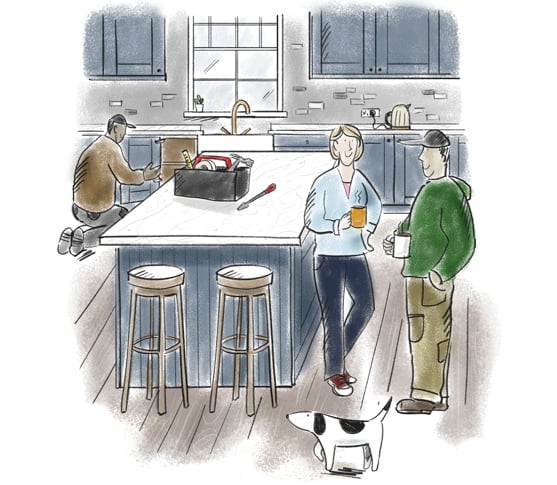
Products
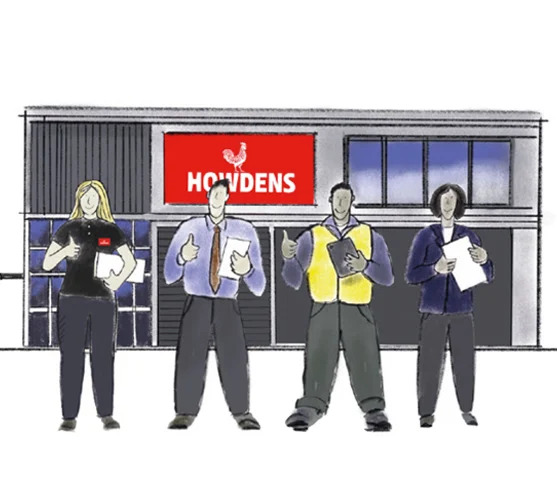
People and Careers

Financial Results
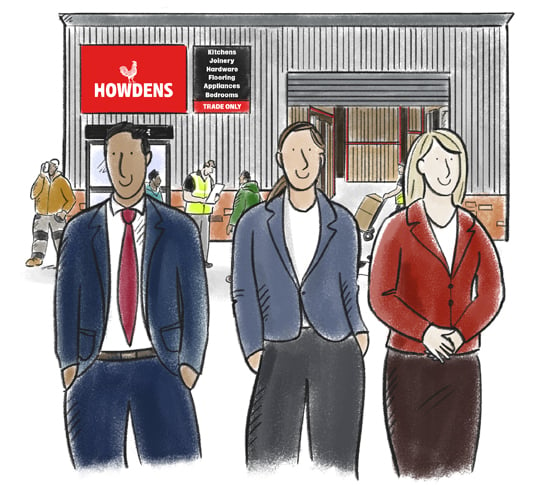